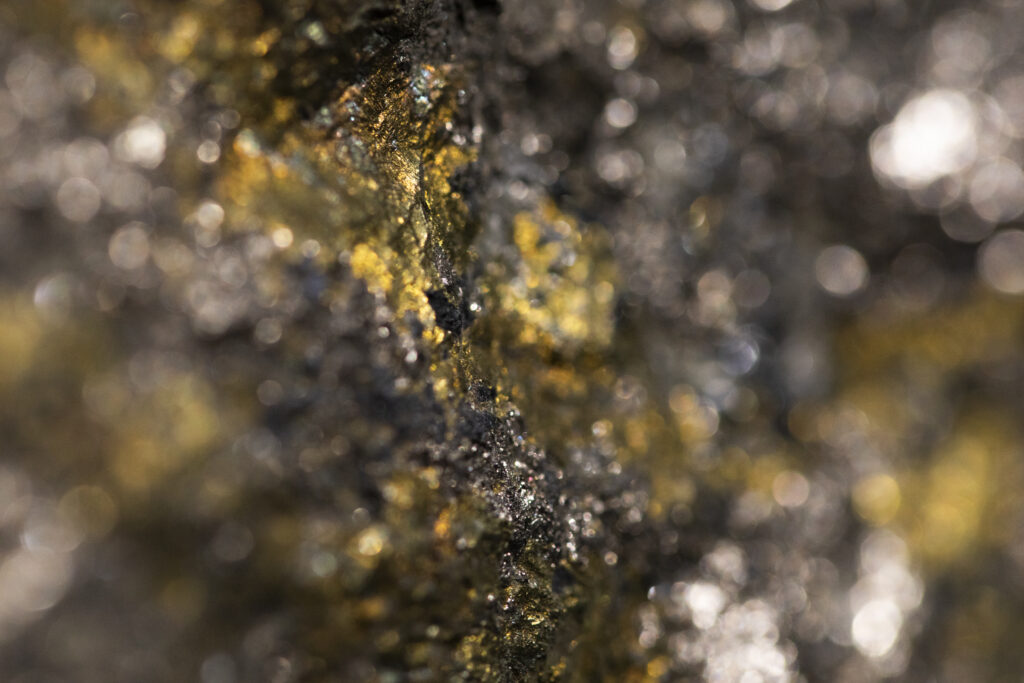
The Metso Research Center is creating a green future for steel and critical metals
Pori is home to a globally unique research facility. With nearly 200 highly qualified experts, it provides answers to the most pressing questions of our time. The research center has just announced a ground-breaking innovation that will cut carbon emissions from steel production by up to 90%.
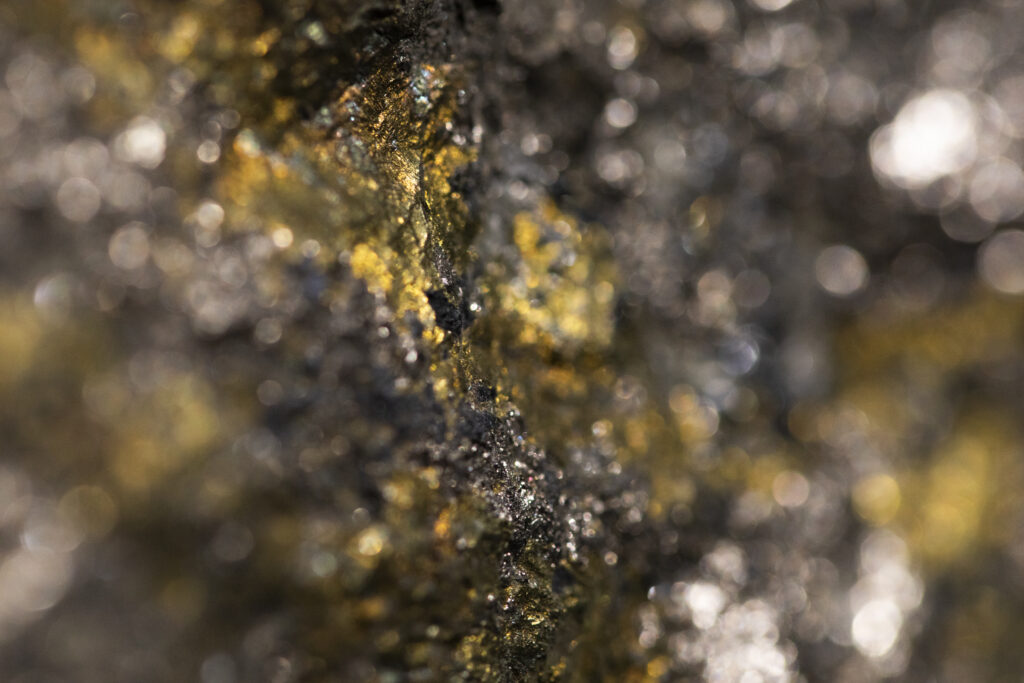
New technology is being created at the facility to recycle the black mass from electric car batteries. Factories that use the black mass are expected to start up within a few years.
Here, the depletion of ore reserves is seen as an opportunity to make mining and minerals processing more ethical and environmentally friendly.
And it is here that investors with an interest in producing critical metals can find help if they are lacking the relevant know-how.
We are at the Metso Research Center, where the above are just a few examples of their extensive innovation expertise.

Electrification has revolutionized Metso Research Center's operations during the past couple of years, say Janne Karonen (left) and Juha Saari, who lead the research work for their business lines at the research center.
Controlling consumption and emissions with Planet Positive solutions
With nearly 200 top experts, the Metso Research Center is an organization that divides the green future of the metals industry into three areas of expertise.
Led by Juha Saari, the R&D team is responsible for the beneficiation processes, which is the stage where the ore leaves the mine. It is crushed and ground. Precious minerals are separated from the ore and recovered.
The resulting concentrate is either sent to the hydrometallurgy R&D team led by Janne Karonen or to the smelting production line represented by Mari Lindgren.
“One of our strengths is that we are able to study the whole process from ore to the final metal, which is very rare. There aren’t many institutions in the world that can do this,” says Juha Saari.
Customer projects, in which the Metso Research Center provides information to support plant investments, make up a significant share of work.
“We have a large portfolio of new and best-performing Planet Positive solutions to reduce water demand, energy consumption and emissions. A technology has to meet these criteria in order to qualify as Planet Positive.”
Customers are increasingly interested in sustainable solutions that are a little more expensive as an investment, but which are sustainable and improve the efficiency of the production process.
The projects vary in size. At its largest scale, the research center covers everything from assessing ore reserves to turnkey deliveries of fully functional plants.
“This is one of our company’s strengths. We aren’t just an equipment supplier; we are able to deliver the entire process and technological solution to the customer. And that is where research plays a key role,” says Juha Saari.
“If we’ve designed the refining process and the plant itself, we can also provide process guarantees.”
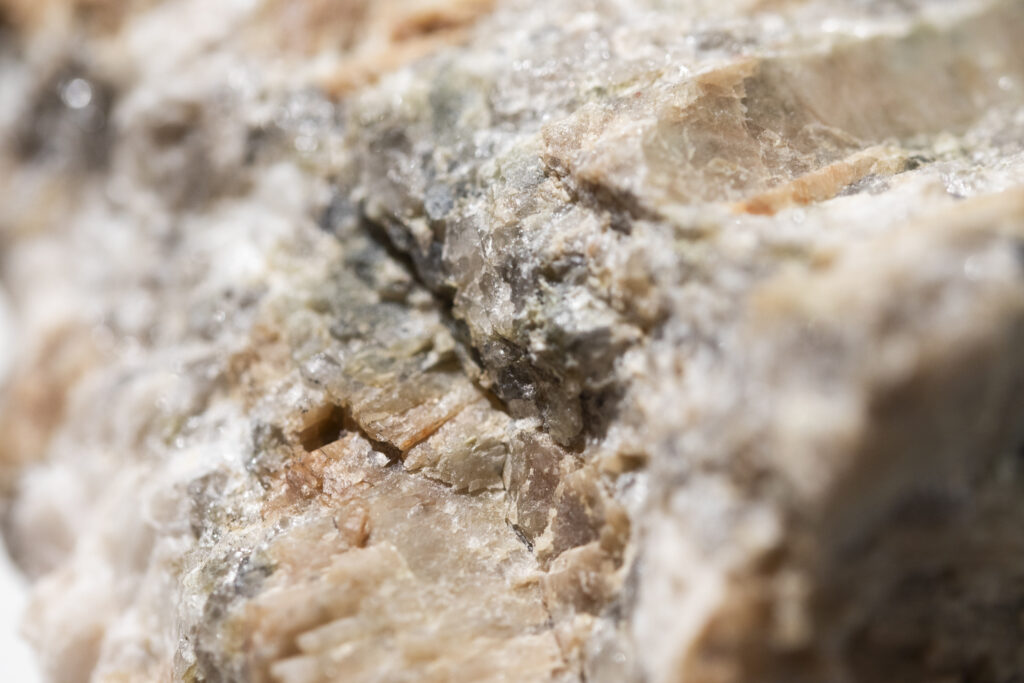
The lithium boom has meant that the research center’s customers will not necessarily come from the mining industry, but instead be investors who purchase comprehensive expertise, from ore reserve assessment to fully operational plants.
Research safeguards electric vehicle production
The rapid increase in electric vehicles, and the subsequent battery boom, have brought about a major change in the research center’s operations over just five years.
More than half of the center’s projects relate to lithium and other battery metals, up from around 10% five years ago.
Of all the battery metals, the teams led by Juha Saari and Janne Karonen work most with lithium.
“The good thing for us is that the research center had already begun researching lithium well before the battery boom. We had a basic knowledge of the different lithium minerals and potential process steps.”
Recycling was also taken into account.
“We have developed process technology for black mass recycling, which is one of the intermediate steps in battery recycling,” says Janne Karonen, giving just one example.
According to Juha Saari, battery recycling is not yet fully economically feasible. .
“But in a couple of years, once the number of batteries is high enough, we can start building the plants. We have an advantage in that respect because the processes are already in place,” he adds.
Copper also plays a key role, as it is an excellent conductor of electricity. Electric vehicles contain four times as much copper as conventional vehicles. It is estimated that copper demand will increase by 50% over the next ten years.
“For the smelting product line, the most significant impact will come from the increased demand for copper, which is required for both electric vehicles and EV charging systems,” says Mari Lindgren.
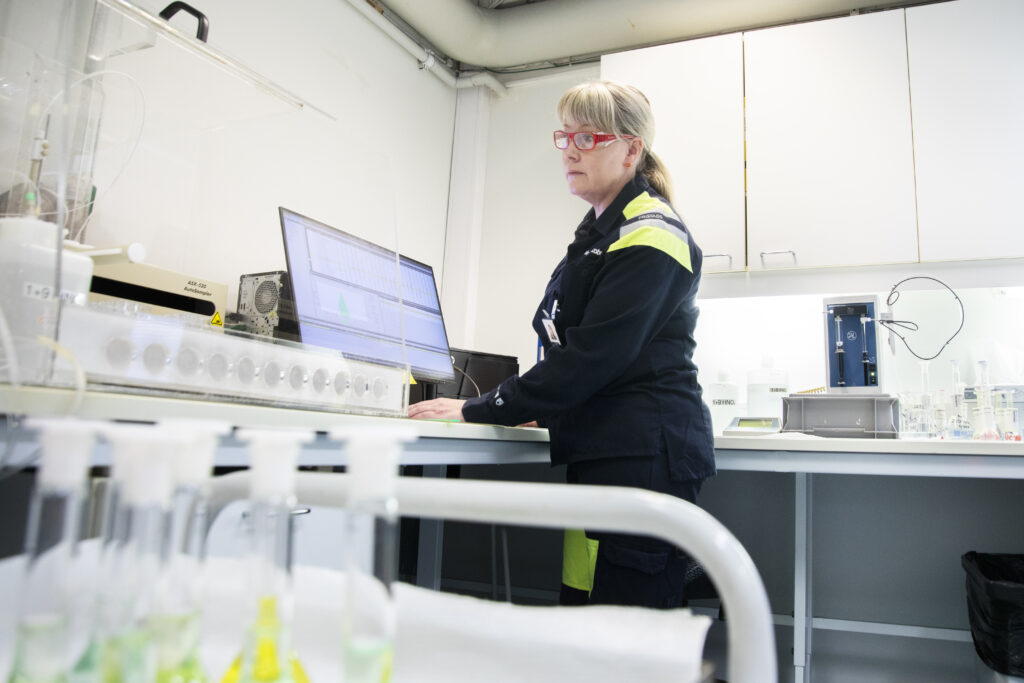
Laboratory supervisor Susanna Wihlman uses ICP testing to determine the concentration of the elements in the sample.
The center’s own pilot plants and chemical analysis
Many companies have cut back their research centers to small test laboratories. Over its 74 years, the Metso Research Center has developed the copper flash smelter, among other things. This process is still used to produce a large share of the world’s copper.
In March, Mari Lindgren’s product line announced a massive breakthrough in green steel production. The technology, designed for the modernization of old steel mills, will reduce carbon dioxide emissions from steel production by 85-90%.
The research center has pilot plants that allow for even large-scale piloting. It also has its own chemical analysis operations to serve all lines of business. The unit also has a comprehensive library of over 19,000 research reports.
“This is a very special excellence cluster on a global scale,” says Juha Saari.
Experimentation at the center is extremely sophisticated.
“Our employees have decades of experience in putting metallurgical theory into practice,” says Janne Karonen.
“We tailor a lot of our technologies to customers’ needs, because we’re currently starting to use new, poorer and recycled raw materials.”
Thanks to Metso Research Center’s expertise, a plant can maintain the usual quality even if the feed material and ore are different.
“It has even been possible to reuse and extract precious metals from tailings, which was once waste that had to be dumped. There have been a few such projects recently,” says Karonen.